Plastic extrusion for tubing, sections, and custom shapes
Plastic extrusion for tubing, sections, and custom shapes
Blog Article
Comprehending the Essentials and Applications of Plastic Extrusion in Modern Production
In the world of modern production, the method of plastic extrusion plays an instrumental duty - plastic extrusion. This elaborate procedure, including the melting and shaping of plastic via specialized dies, is leveraged throughout different sectors for the development of varied products. From auto parts to durable goods product packaging, the applications are vast, and the capacity for sustainability is just as outstanding. Untangling the fundamentals of this process discloses the real adaptability and possibility of plastic extrusion.
The Principles of Plastic Extrusion Refine
While it might appear complicated, the basics of the plastic extrusion procedure are based on fairly straightforward concepts. It is a production procedure in which plastic is thawed and afterwards shaped into a continuous profile with a die. The raw plastic product, frequently in the type of pellets, is fed into an extruder. Inside the extruder, the plastic undergoes warmth and stress, creating it to melt. The molten plastic is then required via a designed opening, known as a die, to develop a long, constant product. The extruded product is cooled and afterwards cut to the preferred size. The plastic extrusion procedure is thoroughly utilized in various industries due to its convenience, performance, and cost-effectiveness.
Different Kinds Of Plastic Extrusion Techniques
Structure upon the fundamental understanding of the plastic extrusion procedure, it is necessary to check out the different methods included in this manufacturing technique. In contrast, sheet extrusion creates big, flat sheets of plastic, which are generally further processed right into products such as food packaging, shower curtains, and cars and truck components. Understanding these methods is essential to utilizing plastic extrusion efficiently in modern production.

The Duty of Plastic Extrusion in the Automotive Sector
An overwhelming majority of components in modern lorries are items of the plastic extrusion process. This procedure has revolutionized the auto market, transforming it right into a more reliable, economical, and flexible production sector. Plastic extrusion is largely utilized in the manufacturing of different automobile elements such as bumpers, grills, door panels, and dashboard trim. The process provides an uniform, constant result, enabling suppliers to produce high-volume components with excellent precision and very little waste. The lightness of the extruded plastic parts adds to the overall decrease in vehicle weight, enhancing fuel performance. In addition, the sturdiness and resistance of these components to warmth, cold, and effect enhance the durability of autos. Hence, plastic extrusion plays an essential duty in useful content automobile production.
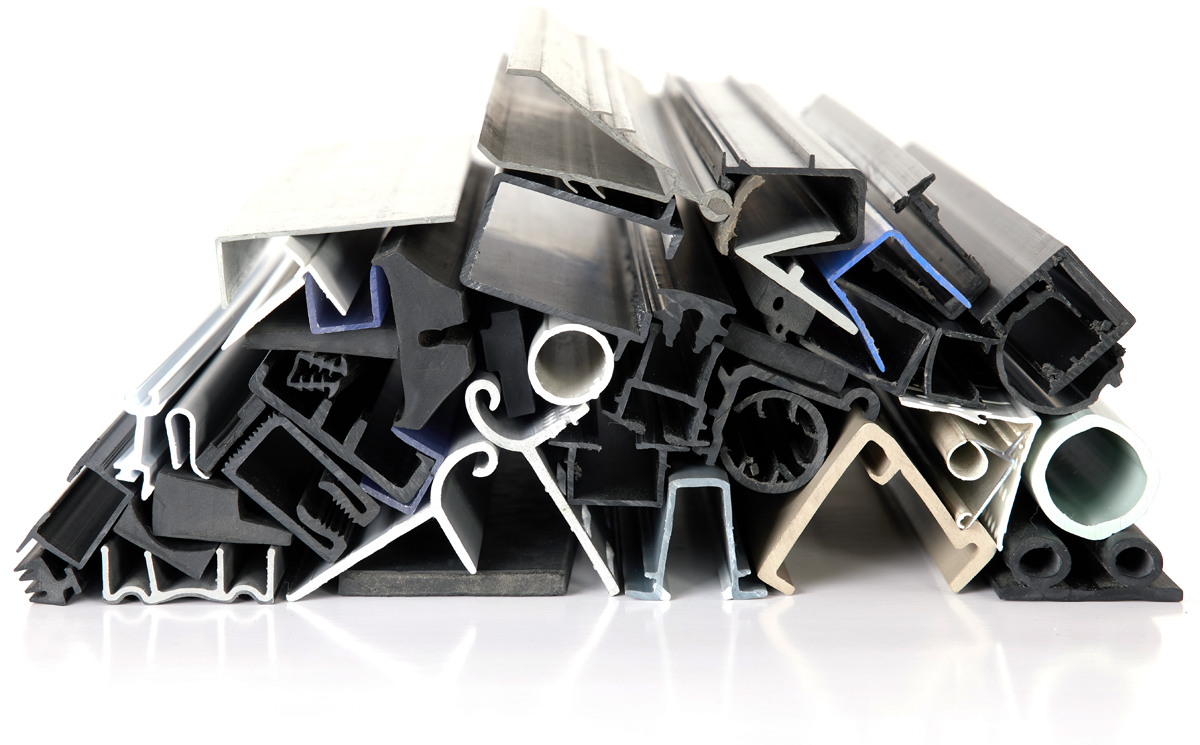
Applications of Plastic Extrusion in Customer Goods Manufacturing
Beyond its considerable effect on the automobile market, plastic extrusion shows equally effective in the realm of customer items making. This procedure is essential in developing a broad variety of items, from food product packaging click for more info to house appliances, toys, and also clinical gadgets. The adaptability of plastic extrusion enables producers to design and generate complicated shapes and sizes with high accuracy and effectiveness. Additionally, because of the recyclability of numerous plastics, squeezed out elements can be reprocessed, reducing waste and expense. The flexibility, flexibility, and cost-effectiveness of plastic extrusion make it a favored choice for several durable goods makers, contributing considerably internet to the sector's growth and technology. The environmental effects of this widespread use require mindful consideration, a topic to be talked about additionally in the subsequent area.
Environmental Effect and Sustainability in Plastic Extrusion
The pervasive usage of plastic extrusion in producing invites analysis of its environmental implications. Reliable equipment lowers power use, while waste monitoring systems recycle scrap plastic, lowering raw product demands. Regardless of these enhancements, further technology is needed to mitigate the ecological footprint of plastic extrusion.
Verdict
In conclusion, plastic extrusion plays an essential role in modern manufacturing, particularly in the auto and consumer goods markets. Recognizing the essentials of this process is vital to optimizing its applications and benefits.
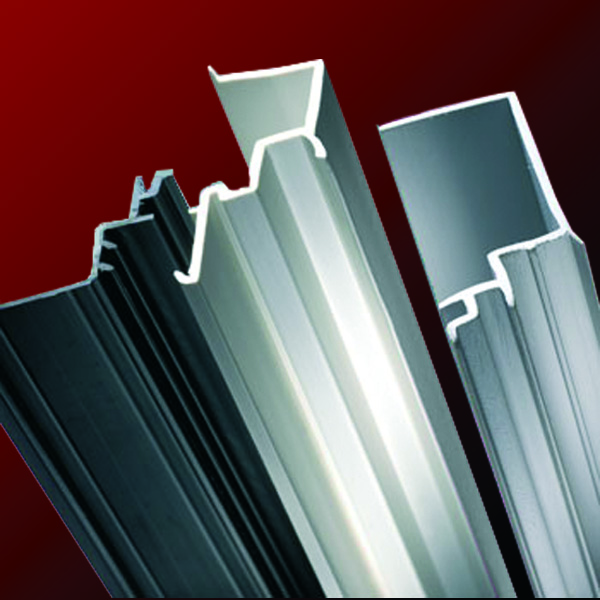
The plastic extrusion process is extensively utilized in various sectors due to its efficiency, versatility, and cost-effectiveness.
Building upon the basic understanding of the plastic extrusion procedure, it is needed to check out the various strategies included in this production technique. plastic extrusion. In comparison, sheet extrusion produces large, level sheets of plastic, which are commonly additional processed right into products such as food product packaging, shower curtains, and vehicle components.An overwhelming bulk of parts in modern automobiles are products of the plastic extrusion procedure
Report this page